Chemicals Used in Sugar Processing
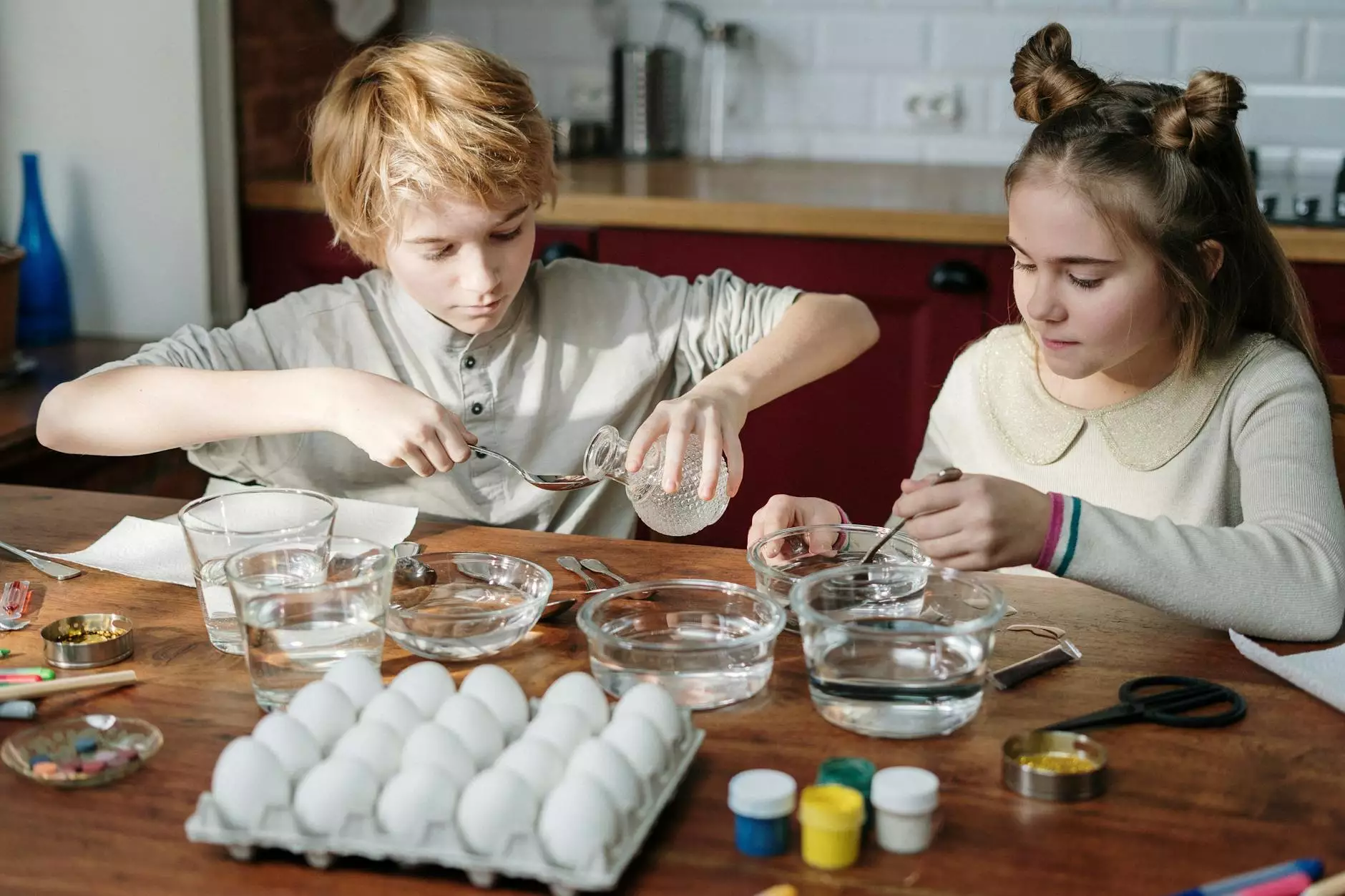
Sugar processing is a complex and vital industry that involves various techniques to extract sugar from sugarcane or sugar beet. The chemical processes not only enhance sugar yield but also ensure quality and safety in the resulting product. This article delves into the chemicals used in sugar processing, their roles, and their significance in the broader context of industrial applications, particularly in water purification services.
1. The Importance of Chemicals in Sugar Processing
The sugar industry relies heavily on a range of chemicals to optimize extraction and refine sugar. These chemicals are instrumental in:
- Enhancing Sugar Yield: Certain chemicals increase the efficiency of sugar extraction from raw materials.
- Purification: They help remove impurities from the raw sugar liquor, ensuring a clean final product.
- Preservation: Chemicals assist in maintaining the quality and shelf-life of sugar during storage and transportation.
2. Key Chemicals Used in Sugar Processing
Several chemicals play crucial roles in the sugar processing industry. Understanding these chemicals is vital for anyone involved in the production and refinement of sugar.
2.1. Lime (Calcium Hydroxide)
Lime is one of the primary chemicals used in sugar processing. It acts as a neutralizing agent in the purification process. When lime is added to the sugar juice, it reacts with impurities, allowing them to precipitate and be easily removed. This process is known as liming, and it results in a clearer and more refined sugar liquor.
2.2. Phosphoric Acid
Phosphoric acid is commonly used for the clarification of sugar juices. It reacts with calcium ions in the presence of lime to form calcium phosphate, which aids in the removal of suspended solids and boosts the effectiveness of the clarification process.
2.3. Sulfur Dioxide
Sulfur dioxide is used primarily as a bleaching agent. It helps in the removal of colorants from sugar solutions, leading to a more appealing final product. It is also effective in controlling microbial growth during processing.
2.4. Activated Carbon
Activated carbon is utilized to absorb and remove colored compounds and impurities from sugar syrup. This chemical is essential for achieving the desired color and taste, making it an integral part of the sugar refining process.
2.5. Antifoaming Agents
During the boiling and evaporation stages of sugar processing, foam may form, leading to inefficiencies. Antifoaming agents are added to prevent foaming, ensuring smooth operation and maximizing yield.
3. The Process of Sugar Refining using Chemicals
The refining process of sugar involves several stages, each employing different chemicals to achieve optimal results. Here is a simplified breakdown:
- Extraction: Sugarcane or beet is crushed, and water is added to dissolve the sugar.
- Clarification: Lime and phosphoric acid are added to the juice, allowing impurities to settle.
- Evaporation: The clarified juice is concentrated to form syrup, where antifoaming agents are used.
- Crystallization: Sugar crystals form during cooling, and activated carbon may be used to improve clarity.
- Centrifugation: The syrup is spun to separate sugar crystals from molasses.
- Drying: Final product drying is crucial to ensure quality.
4. Environmental Considerations in Sugar Processing
As with any industry, the use of chemicals in sugar processing raises environmental concerns. It is essential for sugar manufacturers to implement eco-friendly practices, such as:
- Sustainable Sourcing: Ensuring raw materials are sourced from environmentally responsible suppliers.
- Waste Management: Properly managing waste generated by chemical processes to minimize environmental impact.
- Monitoring and Compliance: Following regulations regarding chemical emissions and waste discharge to protect local ecosystems.
5. Future Trends in Sugar Processing Chemicals
The future of sugar processing chemicals is geared towards innovation and sustainability. Key trends include:
- Biodegradable Chemicals: Research is underway to develop chemicals that are less harmful to the environment.
- Enhanced Efficiency: New formulations that maximize yield while reducing chemical usage.
- Green Technologies: Adoption of technologies aimed at minimizing chemical footprints and promoting sustainability.
6. Role of Water Purification in Sugar Processing
Water is a fundamental resource in sugar processing, not just as a solvent, but also for cooling and washing. Therefore, the quality of water used in sugar processing is critical. Water purification services play an essential role in ensuring that the water meets the necessary standards for sugar production:
- Removal of Contaminants: Water purification processes ensure that impurities do not affect the sugar quality.
- Consistency of Supply: Reliable water suppliers guarantee a steady flow of high-quality water necessary for continual operation.
- Regulatory Compliance: Adhering to local regulations regarding water usage and discharge.
7. Conclusion
In conclusion, the chemicals used in sugar processing are pivotal in ensuring efficiency, quality, and safety in sugar production. Understanding these chemicals and their applications not only benefits producers in optimizing their processes but also lays the groundwork for innovations that can lead to a more sustainable future in sugar processing.
As the industry continues to evolve, water purification services remain a crucial support system, ensuring that sugar producers can operate efficiently, sustainably, and responsibly. Therefore, staying informed about the latest trends and practices in both sugar processing and water treatment is necessary for anyone involved in or entering this vital industry.
chemicals used in sugar processing