Understanding Lubrication Fittings: Essential Insights for Business
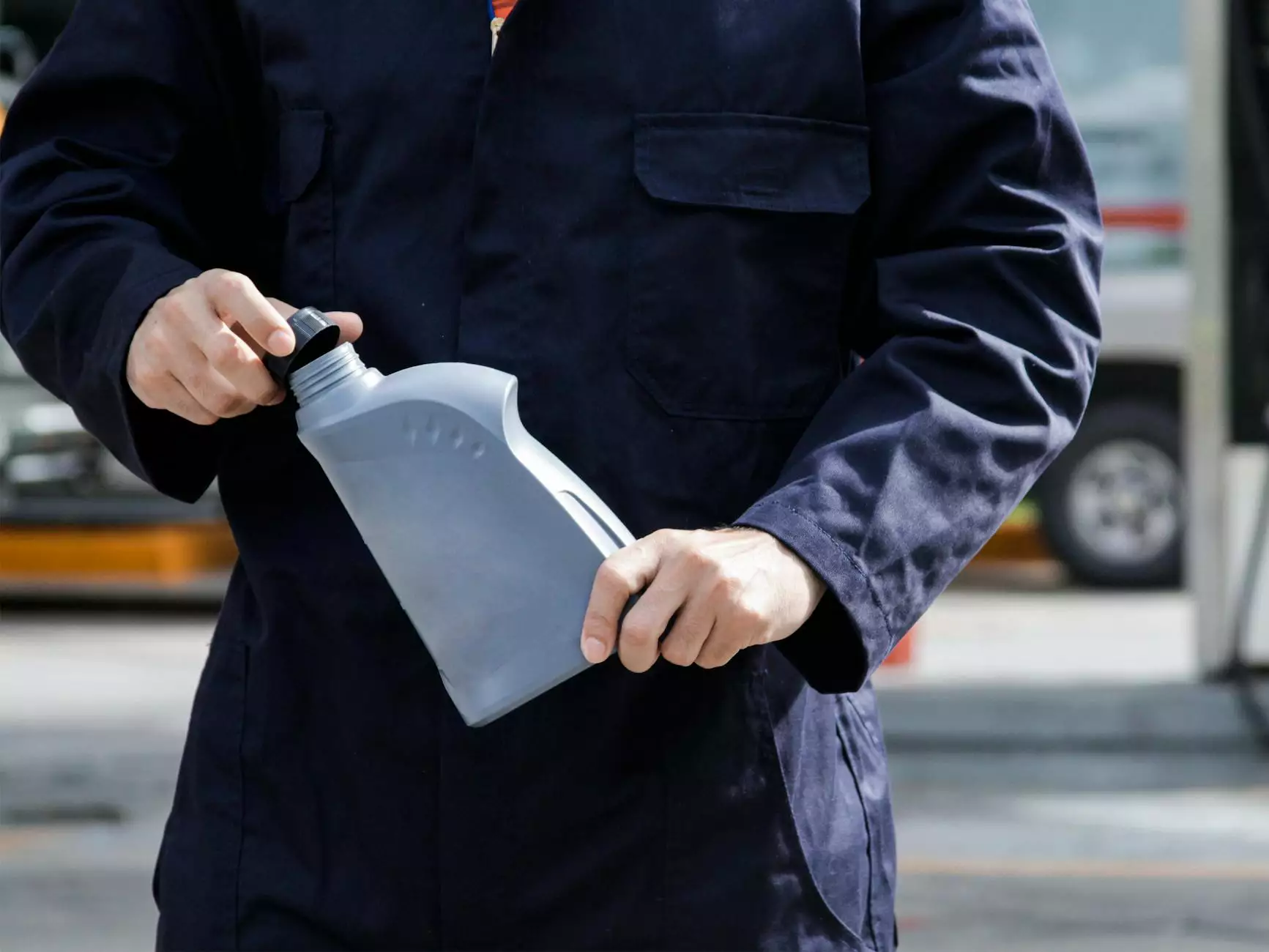
In the realm of industrial maintenance and machinery operation, lubrication fittings play a critical role. Proper lubrication is essential for ensuring the longevity and efficient functioning of any machine or mechanical system. In this extensive article, we will delve into the various types of lubrication fittings, their significance, and the best practices for their maintenance and use. By the end, you will have a comprehensive understanding of how these fittings contribute to optimal business operations.
The Importance of Lubrication in Machinery
Before we dive into lubrication fittings, it’s vital to understand why lubrication is necessary. Lubrication reduces friction between moving parts, which minimizes wear and tear, and helps to dissipate heat generated by machinery. Furthermore, proper lubrication aids in preventing corrosion and contamination, which can significantly shorten the lifespan of equipment.
An effective lubrication system is integral to:
- Extend Equipment Lifespan: Regular lubrication can dramatically increase the operational life of machinery.
- Enhance Performance: Well-lubricated machinery operates more smoothly and efficiently, leading to better performance.
- Reduce Downtime: Preventative lubrication can significantly decrease the likelihood of unexpected equipment failures.
- Lower Operational Costs: By extending equipment life and reducing downtime, businesses can save significant sums in repair costs and lost productivity.
What are Lubrication Fittings?
Lubrication fittings are small mechanical components that facilitate the easy application of lubricant to machinery. They allow for precision lubrication with minimal effort, ensuring that lubrication can be applied in hard-to-reach areas. Typically found on equipment such as bearings, gears, and other moving parts, these fittings are essential in maintaining the overall health and efficiency of mechanical systems.
Types of Lubrication Fittings
There are several types of lubrication fittings, each designed for specific applications and lubrication techniques. Here are the most common types:
- Grease Fittings (Zerk Fittings): Often used in automotive and heavy machinery, these fittings allow for the injection of grease into bearings and other components.
- Screw-in Fittings: These fittings are used in high-pressure applications and are designed to provide a secure and leak-proof connection for lubrication.
- Locking Fittings: These fittings prevent accidental disconnection during operation, ensuring continuous lubrication.
- Flat or Button Fittings: Commonly found on smaller machinery, these fittings are designed for manual lubrication, typically with a grease gun.
Benefits of Using Lubrication Fittings
Incorporating lubrication fittings into your machinery maintenance routine provides numerous benefits:
- Ease of Access: Lubrication fittings can be placed in strategic locations where lubrication is necessary but difficult to reach.
- Consistent Lubrication: Using fittings ensures that a consistent amount of lubricant is applied, optimizing the effectiveness of lubrication.
- Time Efficiency: Quality fittings can reduce the time spent on maintenance tasks, leading to increased productivity.
- Safety: Properly maintained equipment is safer for operators and reduces the risk of accidents caused by equipment failure.
Choosing the Right Lubrication Fitting
Selecting the correct lubrication fitting is crucial for effective maintenance. Here are some factors to consider:
1. Type of Machinery
Different machinery may require specific fittings. Understanding the equipment's design and lubrication requirements is vital.
2. Operating Conditions
Consider the operating temperatures, pressures, and environments (e.g., exposure to chemicals) where the machinery operates. This can dictate the type of fitting and lubricant needed.
3. Lubrication Method
Determine whether you will be using manual or automatic lubrication systems, as this will influence the selection of fittings.
Installing and Maintaining Lubrication Fittings
Proper installation and maintenance of lubrication fittings are essential for ensuring their effectiveness. Follow these steps for best practices:
Installation Steps
- Ensure that the surface is clean and free of debris before installation.
- Use the correct tools to secure the fitting without over-tightening, which can damage the fitting.
- Position the fitting in a way that allows for easy access for lubrication.
Regular Maintenance
Regular maintenance should include:
- Inspections: Check for any signs of damage or wear.
- Cleanliness: Ensure that the fittings remain free of dirt and contaminants.
- Lubrication: Regularly lubricate the fittings to ensure consistent performance.
- Replacement: Replace any damaged or worn fittings promptly to maintain system effectiveness.
Common Issues and Troubleshooting
Even with proper maintenance, issues may arise with lubrication fittings. Here are some common problems and their solutions:
1. Leakage
Leakages can occur due to improper installation or wear. Regularly check and replace any worn-out fittings immediately.
2. Clogging
If a fitting is clogged, disassemble and clean it thoroughly. Use the appropriate solvent for the type of lubricant being used.
3. Over-Lubrication
Adding too much lubricant can cause excess pressure and damage. Always follow manufacturer recommendations regarding lubricant volume.
Innovations in Lubrication Technology
As technology advances, the field of lubrication is seeing innovations that improve the efficiency and effectiveness of lubrication fittings. Some emerging trends include:
- Smart Lubrication Systems: These systems use IoT technology to monitor lubrication levels and alert operators when maintenance is needed.
- Environmentally Friendly Lubricants: With a growing focus on sustainability, many companies are now developing lubricants that are less harmful to the environment.
- Improved Fitting Designs: Innovations in fitting designs enhance accessibility, durability, and reliability.
Conclusion
In conclusion, lubrication fittings are indispensable components within the machinery maintenance industry. Understanding the various types, benefits, and maintenance practices associated with these fittings can significantly enhance the operational efficiency of any business. By prioritizing proper lubrication and adhering to best practices, companies can ensure the longevity and reliability of their equipment, minimizing downtime and reducing costs. As the industry evolves, staying informed about innovations will further benefit businesses in maintaining their machinery effectively.
For all your lubrication fitting needs and other fittings for sale, visit fitsch.cn. Our experts are dedicated to providing high-quality solutions tailored to your specific requirements.