Understanding Pressure Die Casting: An Insight into Die Casting Dies Manufacturers
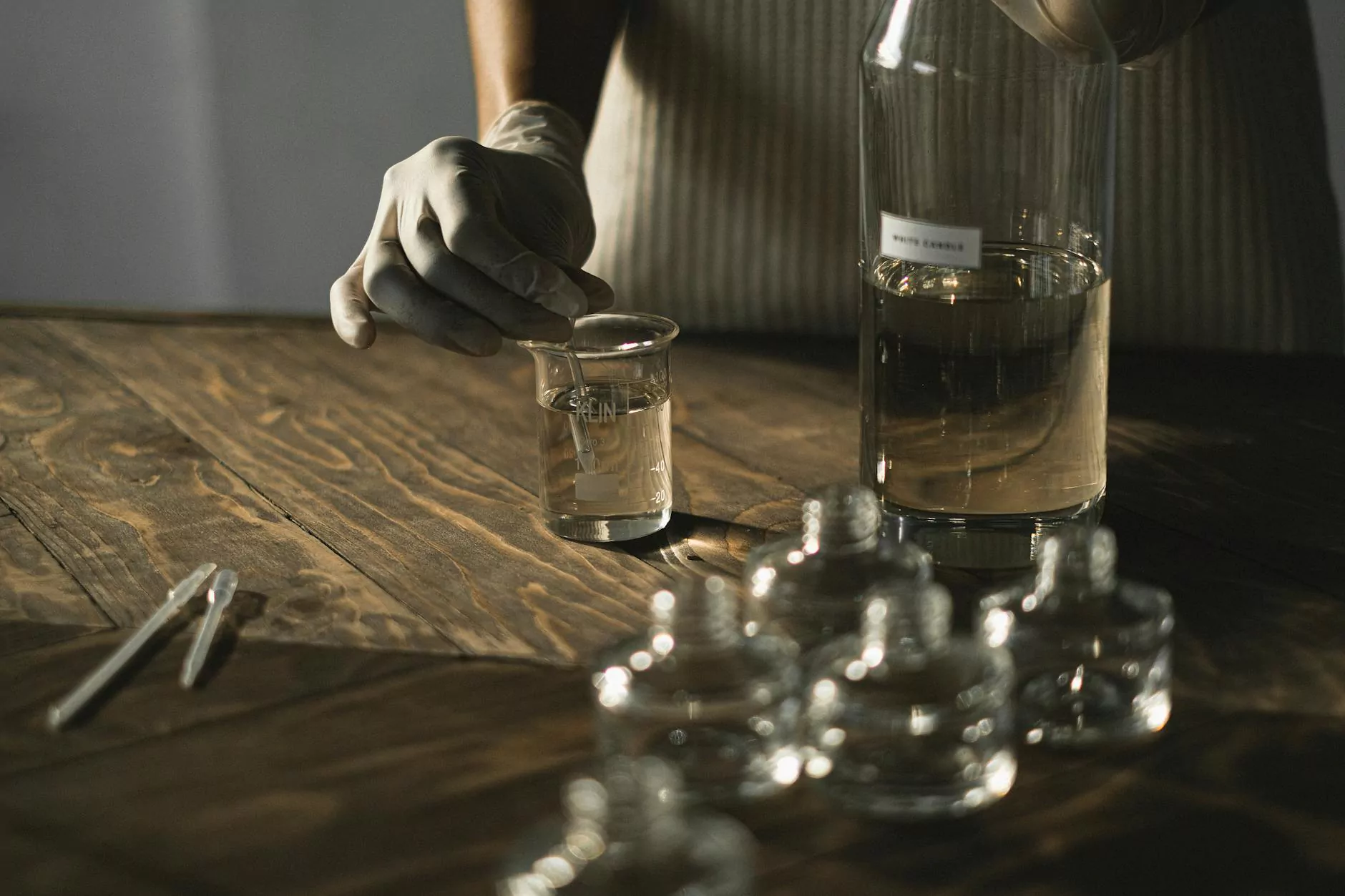
In the world of metal fabrication, few processes stand out as significantly as pressure die casting. This innovative manufacturing process is essential for producing high-quality metal components with precision and efficiency. For industries ranging from automotive to aerospace, the role of pressure die casting dies manufacturers is crucial in ensuring that the entire operation runs smoothly and effectively.
What is Pressure Die Casting?
Pressure die casting is a metal casting process that involves forcing molten metal into a mold cavity. The mold is made from high-quality steel and is designed to withstand the immense pressure applied during the casting process. This method offers numerous benefits, making it a popular choice among manufacturers.
Advantages of Pressure Die Casting
- High Dimensional Accuracy: Products manufactured through pressure die casting exhibit exceptional precision, which reduces the need for further machining.
- Complex Geometries: This process allows for intricate designs that other manufacturing methods struggle to achieve.
- Surface Finish: The resulting surface finish is usually superior, often requiring less post-processing.
- Reduced Material Waste: Pressure die casting uses a minimal amount of raw materials, making it an eco-friendly choice.
- Cost-Effectiveness: Although the initial cost of dies can be high, the reduction in material waste and the speed of production make it economically viable.
The Role of Pressure Die Casting Dies Manufacturers
The backbone of the pressure die casting process is the die itself. As such, pressure die casting dies manufacturers play a pivotal role in the industry. Their expertise in die design and manufacturing directly influences the production quality and efficiency. Here’s why these manufacturers are indispensable:
Expertise in Manufacturing
Manufacturers specialized in pressure die casting possess deep knowledge of metallurgy, engineering, and design. This expertise enables them to create dies that can handle the rigorous demands of the casting process. The quality of the die will ultimately determine the quality of the final product, making the choice of manufacturer essential.
Customization and Innovation
Every industry has unique requirements, and pressure die casting dies manufacturers offer customized solutions tailored to the specific needs of their clients. This flexibility not only optimizes the production process but also adapts to changing market demands. Collaboration between manufacturers and clients leads to innovations, ensuring that the latest technologies are consistently employed.
Quality Assurance
With the high stakes involved in metal fabrication, quality assurance is paramount. Pressure die casting dies manufacturers often implement stringent quality control measures, including:
- Detailed inspections during the manufacturing process
- Material testing to guarantee durability and strength
- Dimensional checks to ensure precision
Applications of Pressure Die Casting
Pressure die casting is utilized in various sectors, each with its specific demands and standards:
Automotive Industry
The automotive sector is one of the most significant users of pressure die casting. Components such as engine blocks, transmission cases, and structural parts benefit from the technique’s precision and strength. Manufacturers can produce lightweight yet durable parts that enhance vehicle performance.
Aerospace Industry
In aerospace, where safety and reliability are critical, pressure die casting offers solutions for producing complex components while meeting stringent regulatory standards. The ability to create intricate designs with high strength-to-weight ratios is especially valuable in this sector.
Consumer Electronics
The consumer electronics industry demands high-quality, aesthetically pleasing components. Pressure die casting allows for sleek designs and excellent surface finishes, making it a popular choice for casings and other structural parts.
Medical Devices
Medical devices require utmost precision and reliability. Components produced via pressure die casting fulfill these requirements, ensuring patient safety and device effectiveness.
The Future of Pressure Die Casting
The future of pressure die casting looks promising, as advancements in technology continue to shape the landscape of manufacturing. Here are a few trends to watch:
Automation and Robotics
The integration of automation and robotics in the pressure die casting process enhances efficiency and consistency. Automated systems can minimize human error and increase production rates, providing manufacturers a competitive edge.
3D Printing and Additive Manufacturing
The rise of 3D printing and additive manufacturing technologies is revolutionizing the way manufacturers approach die design. These technologies enable rapid prototyping and the production of complex geometries that can improve die function and performance.
Eco-Friendly Practices
With growing environmental concerns, pressure die casting manufacturers are increasingly adopting sustainable practices. This includes recycling scrap metal and utilizing environmentally friendly materials in the production process. Such initiatives not only benefit the planet but also resonate with eco-conscious consumers.
Choosing the Right Manufacturer
Selecting the right pressure die casting dies manufacturers is crucial for ensuring the success of your projects. Here are essential factors to consider when making your choice:
Experience and Reputation
Look for manufacturers with a proven track record in the industry. Evaluating their portfolio, client testimonials, and case studies can provide insights into their capability and reliability.
Technology and Equipment
Modern pressure die casting requires advanced machinery and technology. Ensure that the manufacturer utilizes the latest technologies to enhance production efficiency and product quality.
Customer Support and Service
Exceptional customer service can make a significant difference in your experience. Manufacturers should be responsive and willing to collaborate closely with you throughout the production process.
Conclusion
As the metal fabrication industry continues to evolve, the importance of skilled pressure die casting dies manufacturers will only grow. Their expertise not only ensures high-quality production but also drives innovation and efficiency in metal casting processes. By understanding the benefits and applications of pressure die casting and choosing the right partners, businesses can thrive in this competitive landscape.
For more information on advanced metal fabrication solutions, visit DeepMould.net and explore how our range of services can elevate your business.