Mastering Injection Molding Tooling: The Cornerstone of Advanced Metal Fabrication and Manufacturing Success
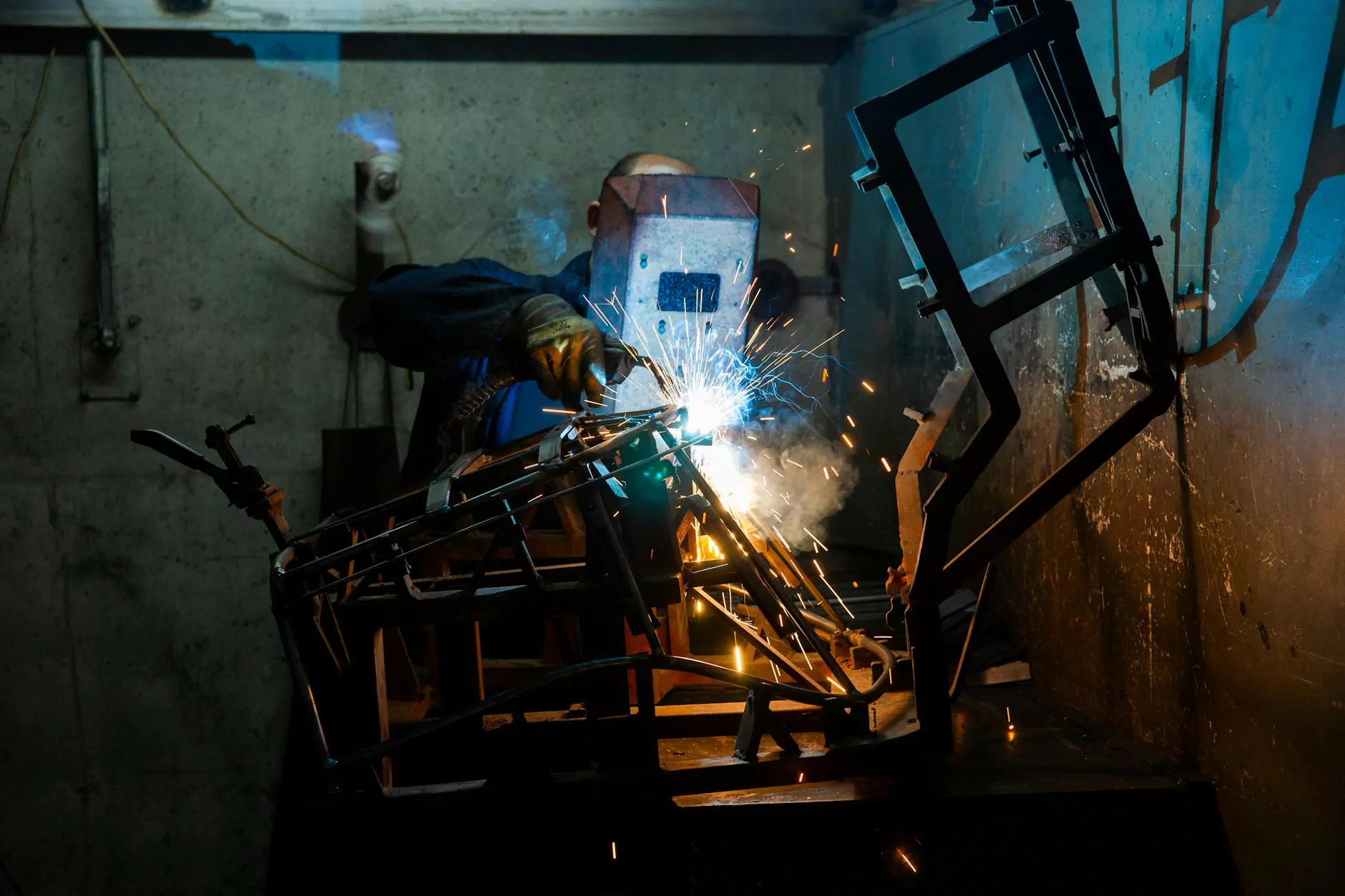
In the competitive landscape of modern manufacturing, injection molding tooling stands as a pivotal element that bridges innovative design with high-volume production. As the backbone of efficient metal fabricators, well-crafted tooling unlocks unparalleled productivity, precision, and cost-effectiveness, empowering businesses to meet soaring market demands. At DeepMould, we are committed to delivering the highest quality injection molding tooling solutions, setting the standard for excellence in the industry.
Understanding Injection Molding Tooling: The Foundation of Modern Manufacturing
Injection molding tooling refers to specialized molds and die setups used to produce complex components from various materials, primarily plastics and metals. These tools are meticulously engineered to shape raw materials into desired forms through precise injection, cooling, and ejection processes. Successful production relies heavily on the quality, design, and durability of the tooling.
Key Components of Injection Molding Tooling
- Core and Cavity: The primary sections that define the internal and external shapes of the finished product.
- Runner System: The channels that guide molten material from the injection unit to the cavities.
- Gate: The entry point where the material flows into the cavity; its design affects surface finish and product quality.
- Cooling System: Embedded channels and passages that regulate the temperature for consistent molding cycles.
- Ejector System: Mechanisms that release the finished parts from the mold without damage.
The Significance of High-Quality Injection Molding Tooling in Metal Fabrication
For metal fabricators, the deployment of superior injection molding tooling is transformational. It enables the mass production of intricate metal components with exceptional precision, repeatability, and durability. This technological backbone reduces waste, shortens lead times, and lowers manufacturing costs—factors that are crucial in today’s fast-paced industrial environment.
Advantages of Investing in Premium Injection Molding Tooling
- Enhanced Product Accuracy: Precision-engineered molds ensure tight tolerances, vital for complex metal parts used in aerospace, automotive, and electronics industries.
- Improved Production Efficiency: Durable tooling reduces downtime and maintenance, allowing for continuous, high-volume output.
- Consistency and Repeatability: High-quality molds produce uniform parts every cycle, essential for components requiring strict quality standards.
- Cost Savings: While initial investment may be higher, the longevity and reliability of top-tier tooling significantly decrease overall manufacturing expenses.
- Design Flexibility: Advanced tooling can accommodate complex geometries, multiple cavities, and intricate detailing with ease.
Design and Manufacturing Process of Injection Molding Tooling
The journey to creating durable and precision injection molding tooling involves several meticulously executed steps:
1. Product Design and Prototyping
Critical analysis of the product design, including material selection, structural requirements, and functional specifications. CAD modeling facilitates an accurate virtual prototype, allowing for early detection of potential issues.
2. Mold Design & Engineering
Our expert engineers translate the product design into detailed mold blueprints, considering factors like thermal management, demolding techniques, and material flow. Advanced simulation software helps optimize the molding process prior to fabrication.
3. Material Selection for Molds
The choice of mold materials impacts durability and precision. Common choices include high-grade steels such as P20, H13, or S136, depending on production volume and operational conditions.
4. Manufacturing & Machining
The manufacturing process involves high-precision CNC machining, electrical discharge machining (EDM), and polishing techniques to achieve intricate details and smooth surface finishes.
5. Assembly & Quality Control
Assembled molds undergo rigorous testing, including leak detection, thermal cycling, and dimensional inspection, to ensure alignment with strict quality standards before deployment.
Innovations and Trends in Injection Molding Tooling
The field of injection molding tooling is continually evolving, driven by technological innovations that foster greater efficiency and sustainability. Some of the notable trends include:
- Rapid Tooling: Utilizing additive manufacturing techniques like 3D printing for quick prototype development, reducing lead times significantly.
- Hot Runner Systems: Minimizing material waste and cycle time by maintaining consistent temperature regulation within the runner system.
- Artificial Intelligence & Automation: Integrating AI algorithms for predictive maintenance, process optimization, and quality assurance.
- Eco-Friendly Materials: Developing molds that support biodegradable or recyclable materials, aligning manufacturing practices with environmental sustainability.
- Advanced Materials for Molds: The development of wear-resistant, corrosion-proof steels prolongs mold life and reduces downtime.
Choosing the Right Partner for Injection Molding Tooling Needs
The path to manufacturing excellence depends greatly on selecting an experienced metal fabricator with comprehensive capabilities in injection molding tooling. The ideal partner should offer:
- Custom Design Expertise: In-depth understanding of diverse project requirements and innovative design solutions.
- Material Knowledge: Extensive experience with different mold materials suitable for specific applications.
- Advanced Machinery: State-of-the-art CNC machines, EDM, and surface finishing tools.
- Quality Assurance: Rigorous testing protocols, adherence to industry standards (ISO, ASME), and certification.
- End-to-End Service: From initial concept to final production, including prototyping, mold fabrication, testing, and ongoing maintenance.
The DeepMould Advantage: Excellence in Injection Molding Tooling & Metal Fabrication
At DeepMould, we stand out by offering unparalleled expertise in injection molding tooling tailored to meet the complex demands of various industries. Our commitment includes:
- Cutting-Edge Technology: Leveraging the latest CNC machining, EDM, and simulation software to deliver high-precision molds.
- Customized Solutions: Approaching each project with a unique strategy to optimize form, function, and cost-effectiveness.
- Material Durability: Using premium-grade steels and composites that withstand demanding production cycles.
- Superior Quality Control: Implementing comprehensive inspection procedures to ensure each mold meets strict standards.
- Expert Team Support: Collaborating with industry experts to refine designs, troubleshoot issues, and improve manufacturing processes.
Beyond Injection Molding Tooling: Broader Impact on Manufacturing and Industry Growth
The development and deployment of high-quality injection molding tooling catalyze significant advancements across multiple sectors:
- Automotive Industry: Facilitates mass production of durable, lightweight metal and plastic components integral to vehicle safety and performance.
- Electronics & Consumer Goods: Powers the creation of intricate, miniaturized parts essential for modern electronic devices.
- Medical Devices: Ensures high-precision molds that uphold rigorous sterility and safety standards.
- Aerospace & Defense: Provides the precision and reliability needed for critical aerospace components with complex geometries.
By investing in advanced injection molding tooling, companies unlock opportunities for innovation, scalability, and global competitiveness, all while enhancing sustainability and operational efficiency.
Conclusion: Elevate Your Manufacturing with the Right Injection Molding Tooling Partner
In conclusion, robust, innovative, and precision-engineered injection molding tooling is fundamental to achieving manufacturing excellence. Companies seeking to improve product quality, streamline production, and maintain competitive edge should prioritize partnering with experienced, technology-driven metal fabricators like DeepMould. Our unwavering dedication to quality, innovation, and customer satisfaction positions us as leaders in the field, ready to support your project from concept to production excellence.
Explore how we can transform your manufacturing processes with superior injection molding tooling solutions. Contact us today to learn more about our comprehensive services and how we can help you succeed in an increasingly demanding market environment.